Bronze 12
The CuSn12 is a high-performance alloy in the mechanical applications of wear parts. It has excellent characteristics for the casting of very complex moulds, which make it an excellent candidate for the production of raw products. Easy to work and weld is a versatile material.
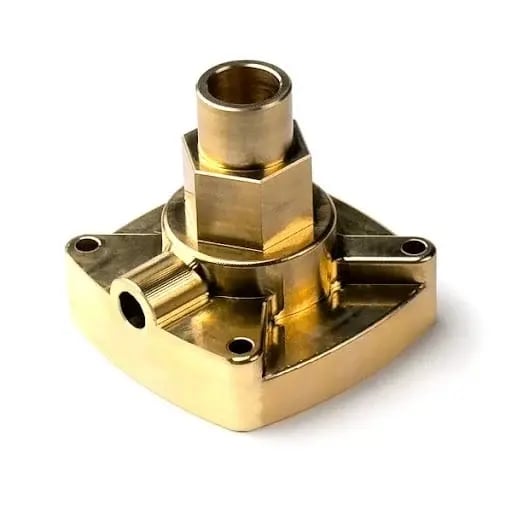
PROS
- Highly marine corrosion resistant
- High friction, wear or pressures resistant
- Good mechanical strength
CONS
- Expensive
- Heavy
MAIN FEATURES
- Process: CNC Machining
- Tolerances: ISO 2768-1 fine (f) or medium (m) class. Info
- Max size: 300x300x50mm ; 12x12x2 in
- Lead time: <4 days
BRONZE CUSN12 CNC MACHINED GALLERY
BRONZE 12 COMMENT
CuSn12 bronze emerges as an ideal alloy for mechanical applications requiring superior resistance to friction and wear. This alloy is widely used in components subject to intense mechanical stress, such as bushings mounted on motion axles and shafts, where durability and reliability are critical to the proper functioning of machines and systems.
Pros
Marine corrosion resistance: CuSn12 bronze offers excellent resistance to marine corrosion, making it an ideal choice for applications in maritime environments. Its ability to resist corrosion caused by salt water and weathering ensures durability and reliability in the most demanding conditions, contributing to the longevity of structures and equipment used offshore.
Friction and wear resistance: Due to its high resistance to friction and wear, CuSn12 is particularly suitable for mechanical components subject to intense stress, such as bushings. These components offer a strong and durable sliding surface, reducing friction and wear during axis movement and ensuring smooth and reliable machine operation.
Mechanical strength: Bronze alloy has good mechanical strength, ensuring reliable performance over time even under mechanical loads and stresses. This strength contributes to the durability and robustness of the components, ensuring a long service life and reducing the need for maintenance and replacement.
Cons
Expensive: It is important to consider that Bronze 12 may cost more than other alloys due to its superior properties, such as corrosion resistance and high wear resistance. However, this initial cost can often be offset by the superior durability and reliability offered by the alloy, reducing maintenance and replacement costs in the long run.
Heavy: The density of bronze alloy makes it relatively heavy compared to other alternatives, which may limit its use in applications where weight is a critical factor. However, it is important to carefully evaluate the specific needs of the application and consider the advantages of CuSn12's strength and durability over its additional weight. In many situations, the performance benefits of the alloy may offset its weight, making it an advantageous choice.
Applications
Bushings for motion axles and shafts in industrial and marine machinery: Bushings made of the alloy CuSn12 provide support and friction reduction in the motion axles and shafts of industrial and marine machinery. Thanks to its resistance to wear and friction, CuSn12 bronze ensures smooth and reliable operation of machinery even under severe working conditions.
Supports and bearings for machinery and equipment subject to wear and friction: CuSn12 bronze is also used in the production of supports and bearings used in machinery and equipment subject to wear and friction. These components provide stability and friction reduction, helping to extend equipment life and maintain high operational performance over time.
Boat parts and coastal structures in corrosive marine environments: Due to its exceptional corrosion resistance, CuSn12 bronze is used in the manufacture of parts and components for boats and coastal structures exposed to corrosive marine environments. These parts include structural components, anchoring accessories and propulsion system parts, ensuring corrosion resistance and long life in aggressive marine environments.
Conclusion
In conclusion, CuSn12 bronze proves to be a reliable and durable choice for a wide range of industrial and marine applications. Its resistance to marine corrosion, high friction and wear resistance, and good mechanical strength make it particularly suitable for components subject to intense stress, such as bushings and mechanical bearings. Although it may entail a higher initial cost and a relatively high density, the performance advantages offered by the alloy more than compensate for these factors, ensuring optimal equipment operation and longer life. Ultimately, CuSn12 bronze remains a preferred choice for projects requiring superior quality, reliability and performance.
MATERIAL PROPERTIES
Tensile breaking load | 275 MPa |
Modulus of elasticity | 110 GPa |
Elongation at break | 9% |
Density | 8,60 g/cm³ |
Melting temperature | 920 ºC |
Hardness | 90 Brinell |
Yield Strength | 145 MPa |
At Weerg, we pride ourselves on providing fast, reliable and amazing customer service. We believe that this is what distinguishes great companies from others.
Questions and answers
Bronze is an alloy primarily composed of copper and tin, with possible additions of other elements such as zinc, lead, or nickel to enhance specific properties. CuSn12 bronze, in particular, contains 12% tin, which gives it excellent corrosion resistance, high mechanical strength, and durability. It is known for its ability to withstand wear, high friction, and high pressures, making it a versatile and reliable material for industrial and mechanical applications.
No, bronze is not magnetic. Being primarily composed of copper and tin, which are non-ferromagnetic materials, it does not exhibit magnetic properties. This characteristic makes it ideal for applications where the absence of reactions to magnetic fields is important, such as in electronic components or sensitive equipment.
Bronze is widely used in various applications due to its corrosion resistance, wear resistance, and ability to handle high pressures. It is commonly employed in the manufacture of pumps, valves, bearings, bushings, and mechanical parts subject to high friction. Its ability to resist oxidation and mechanical stresses makes it ideal for industrial machinery, marine equipment, and components operating in corrosive or high-load environments. Additionally, bronze is often chosen for decorative objects, musical instruments, and coins due to its workability and aesthetic appeal.
The main difference between brass and bronze lies in their composition. Bronze is an alloy of copper and tin, while brass is an alloy of copper and zinc. This distinction is reflected in their mechanical properties and appearance: bronze is generally harder, more wear-resistant, and corrosion-resistant, whereas brass is softer, easier to work with, and has a brighter, golden appearance. Bronze is preferred for applications requiring structural strength and durability, while brass is often used for decorative components and applications where electrical conductivity and workability are more important.
Bronze, particularly CuSn12, has high mechanical strength, making it suitable for high-performance applications. Its tensile strength can range from 250 to 400 MPa, depending on treatment and processing, while its Brinell hardness can reach values of approximately 90-120 HB. These characteristics allow bronze to withstand high loads, intense friction, and significant pressures, making it a durable and reliable material for technical and industrial components.
QUOTE IN 3 SECONDS WITHOUT COMMITMENT
Do you want to turn your 3D project into reality?
Upload your 3D file to get one step closer to manufacturing your parts.
free instant quote