PETG ESD
The addition of carbon nanotubes to ESD PETG significantly enhances the material’s electrostatic dissipation properties, while maintaining the key characteristics of PETG. This unique combination makes it ideal for critical applications in sectors such as electronics or ATEX atmospheres, where protection against electrostatic discharge is essential.
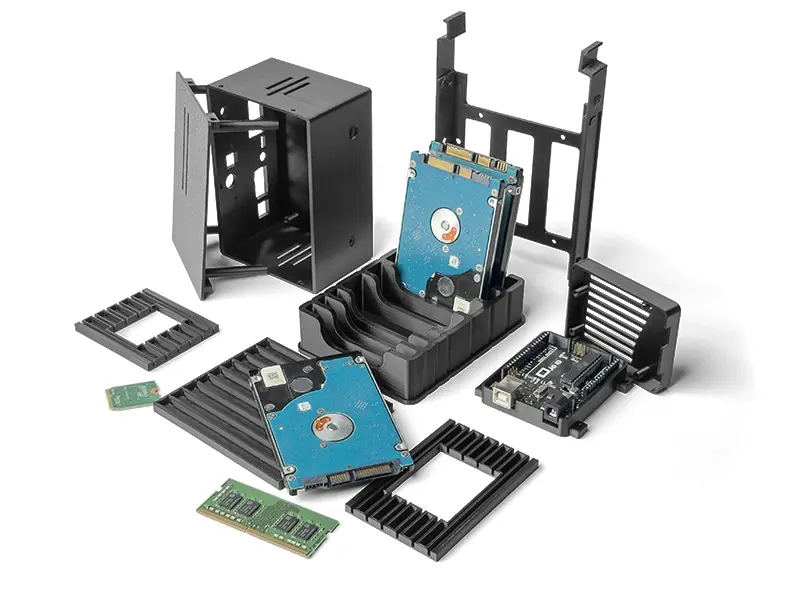
PROS
- Antistatic properties
- Good resistance to oils and greases
- Good impact resistance
CONS
- Limited heat resistance
- Higher cost compared to unfilled PETG
MAIN FEATURES
- 3D printing process: FDM
- Tolerances: ±0,60mm < 100mm ; ±0,6% > 100mm
- Max size: 250 x 250 x 250 mm; 9,8 x 9,8 x 9,8 in
- Lead time: <3 days
PETG ESD 3D PRINTING VIDEO GALLERY
Antistatic Properties
The antistatic properties of ESD PETG are crucial for applications sensitive to electrostatic discharge. The integration of carbon nanotubes reduces surface resistance, enabling the dissipation of accumulated charges. This is vital in industries such as electronics, where discharges can damage delicate components, and in ATEX environments, where it prevents hazardous sparks. The stability of these properties ensures consistent protection, enhancing the reliability of products made with ESD PETG.
Good Resistance to Oils and Greases
ESD PETG offers excellent resistance to oils and greases, making it ideal for industrial environments exposed to oily substances. The PETG matrix prevents the penetration of contaminants, preserving the material’s mechanical properties and structure. This characteristic is particularly useful in sectors such as automotive and the food industry, where chemical resistance prolongs the lifespan of components and reduces the need for maintenance, thereby increasing the versatility of ESD PETG.
Good Impact Resistance
ESD PETG maintains high impact resistance, thanks to the intrinsic properties of unfilled PETG and the addition of carbon nanotubes. This allows the material to effectively absorb and dissipate the energy from impacts, preventing damage and deformation. Impact resistance is crucial in operational environments where components may be subjected to sudden mechanical stresses, such as in production lines or in the automotive and aerospace sectors. Consequently, ESD PETG ensures durability and safety, reducing replacement and maintenance costs.
QUOTE NOW YOUR PARTS
FREE INSTANT QUOTEPETG FILAMENT IMAGE GALLERY
COMMENT
In the panorama of advanced plastic materials, ESD PETG represents an innovative solution that combines the intrinsic characteristics of PETG with additional electrostatic dissipation properties. PETG, an acronym for Polyethylene Terephthalate Glycol, is known for its impact resistance and ease of processing, making it a preferred material in numerous industrial and commercial applications. However, the introduction of carbon nanotubes into PETG has enhanced its antistatic capabilities, transforming it into a material particularly suitable for sectors that require effective management of electrostatic charges.
Advantages
One of the main advantages of PETG ESD is its excellent electrostatic dissipation capacity. The incorporation of carbon nanotubes imparts a lower surface resistance to the material than traditional plastic materials, allowing for rapid dissipation of electrostatic charges that may accumulate during use of the component. This feature is particularly crucial in electronic applications, where the presence of electrostatic discharges can damage sensitive components or compromise the operation of complex devices.
In addition to its antistatic properties, PETG ESD maintains the good mechanical characteristics typical of PETG. The material has a remarkable impact resistance, with a Charpy impact strength of 5.7 kJ/m², making it suitable for withstanding impacts and mechanical stresses without easily deforming or breaking. This factor is essential in industrial environments where components may be subject to accidental impacts or harsh operating conditions.
Another advantage is its good resistance to oils and greases. The PETG matrix gives the material the ability to resist the penetration of oily and greasy substances, making it ideal for applications in industrial environments where such contaminants are common. This chemical resistance broadens PETG ESD's range of use, allowing it to be used in contexts that require greater durability and resistance to aggressive chemical agents.
Disadvantages
Despite its numerous advantages, this material also presents some disadvantages that limit its adoption in certain applications. One of the main limitations is heat resistance. With a Heat Deflection Temperature (HDT) of only 76 °C, ESD PETG can deform or lose its mechanical properties under high thermal loads. This limits its use in applications that require high thermal stability, such as some automotive components or devices operating in high-temperature environments.
Another negative aspect is the high cost of ESD PETG compared to unfilled PETG. The integration of carbon nanotubes results in increased production costs, making the material less competitive in terms of price compared to traditional plastic materials. This can be an obstacle for companies looking for cost-effective solutions, especially in highly cost-sensitive sectors.
Applications
ESD PETG is utilised across a wide range of sectors, thanks to its antistatic and mechanical properties. One of the primary applications is in electronics, where the material is used to produce components that require protection against electrostatic discharges. For example, enclosures for electronic devices, printed circuit board components and housings for sensitive equipment benefit from the dissipative properties of ESD PETG, ensuring greater longevity and reliability of the final products.
Another relevant area is ATEX environments, where protection against electrostatic discharges is essential to prevent explosions in potentially hazardous areas. In such contexts, ESD PETG is used to manufacture machinery components, housings for monitoring devices and other applications that require intrinsically safe and antistatic materials.
Furthermore, this material is used in applications involving friction components, where impact resistance and electrostatic charge dissipation are crucial. For instance, moving parts of industrial machinery, cable supports and automation system components benefit from the properties of ESD PETG, improving their efficiency and service life.
Comparison with other materials
PETG Standard
Standard PETG is renowned for its ease of printing and good impact resistance, making it a popular choice for many general applications. However, unlike ESD PETG, standard PETG does not possess intrinsic antistatic properties. This means that in applications where the dissipation of electrostatic charges is crucial, such as in electronics or ATEX environments, standard PETG may not offer the necessary protection. Furthermore, while both materials share good mechanical properties and impact resistance, ESD PETG adds an additional level of functionality without compromising its mechanical characteristics, thereby justifying its higher cost in specific contexts.
ABS (Acrylonitrile Butadiene Styrene)
ABS is another widely used material for 3D printing, valued for its robustness, thermal resistance and ease of processing. However, ABS does not possess antistatic properties, making it less suitable for applications that require the management of electrostatic charges. Although ABS offers good mechanical resistance, ESD PETG provides a better balance between impact resistance, electrostatic dissipation and chemical resistance, making it a more versatile choice for specific industrial applications.
PLA (Polylactic Acid)
PLA is one of the most popular materials for 3D printing thanks to its ease of use, biodegradability, and good surface quality. However, PLA presents several limitations compared to ESD PETG. Firstly, PLA has lower impact resistance and reduced thermal stability, with a significantly lower Heat Deflection Temperature (HDT) than ESD PETG. Although PLA is excellent for prototypes and decorative models, ESD PETG proves superior for functional applications that require durability, mechanical strength and electrostatic charge management.
Nylon
Nylon is a robust and flexible material, know for its mechanical and tensile strength. However, Nylon can be more challenging to print, requiring more precise printing conditions and sometimes necessitating post-treatments to enhance its surface properties. Although Nylon is excellent for applications that demand flexibility and strength, ESD PETG combines these characteristics with electrostatic dissipation, offering a significant advantage in specific sectors such as electronics and ATEX environments.
Conclusion
ESD PETG emerges as an advanced plastic material that offers a balanced combination of mechanical and dissipative properties, making it particularly suitable for applications in critical sectors such as electronics and ATEX environments. Its ability to dissipate electrostatic charges, combined with impact resistance and good resistance to oils and greases, makes it an ideal choice for components that must operate in complex and potentially hazardous industrial settings.
However, it is important to consider the limitations of ESD PETG, such as its relatively low heat resistance and higher cost compared to traditional plastic materials. These factors can influence the decision to use it in contexts where thermal management is crucial or where production costs need to be tightly controlled.
A comparison with other antistatic materials highlights how ESD PETG positions itself as a premium solution, offering superior performance in terms of mechanical resistance and electrostatic dissipation at a higher cost. This characteristic makes it particularly suitable for applications where performance and reliability take precedence over cost.
In conclusion, ESD PETG represents a technologically advanced solution for specific needs in electrostatic dissipation and mechanical resistance. Its adoption in critical sectors underscores the importance of specialised materials to ensure the safety and reliability of components in complex environments. Despite some limitations, the potential offered by ESD PETG makes it a highly valuable material for the future of the plastics industry.
Properties of ESD PETG
Tensile breaking load | 36,1 MPa |
Modulus of elasticity | 1983 MPa |
Elongation at break | 7,3% |
HDT 0.45 MPa | 76°C |
Charpy impact resistance | 5,7 kJ/m² |
Questions and answers
PETG filament is a thermoplastic material mainly used in 3D printing. PETG stands for Polyethylene Terephthalate Glycol and is a modified variant of PET (Polyethylene Terephthalate). The PETG filament combines the ease of printing of PLA with the strength and durability of ABS, offering good impact resistance and chemical resistance. It is valued for its versatility and superior mechanical properties compared to other common filaments, making it a popular choice for a wide range of 3D printing applications, both domestic and industrial.
The main difference between PETG and ESD PETG lies in the addition of carbon nanotubes to standard PETG to create ESD PETG. This modification imparts the material with electrostatic dissipation properties, making it antistatic. While traditional PETG is known for its impact resistance and ease of processing, ESD PETG maintains these characteristics while adding the ability to manage electrostatic charges. This difference makes ESD PETG particularly suitable for applications in environments sensitive to electrostatic discharges, such as electronics and ATEX atmospheres.
Yes, ESD PETG is considered safe when used correctly in the applications for which it was designed. The presence of carbon nanotubes grants the material electrostatic dissipation properties without compromising the mechanical and chemical safety of PETG. However, as with any plastic material, it is important to ensure that ESD PETG is used within the limits of its technical specifications, especially in terms of temperature and chemical resistance, to guarantee optimal performance and prevent potential risks related to overloads or extreme operating conditions.
PLA (Polylactic Acid) and PETG (Polyethylene Terephthalate Glycol) are both popular materials used in 3D printing, but they exhibit significant differences that make them suitable for various applications. PLA is renowned for its ease of printing, offering a smooth and glossy finish with excellent detail resolution, making it ideal for creating prototypes, decorative objects, and models where aesthetic quality is paramount. However, PLA is more brittle and has lower impact resistance compared to PETG, which can limit its use in functional parts that require durability.
On the other hand, PETG combines the typical ease of printing associated with PLA with enhanced mechanical properties similar to ABS, providing greater flexibility and impact resistance. This makes PETG a better choice for producing functional components, mechanical parts, and objects that need to withstand stress and wear. Additionally, PETG has superior chemical resistance. While PLA is biodegradable and derived from renewable resources, making it environmentally sustainable, PETG offers greater longevity and robustness, making it suitable for applications that require both strength and reliability.
ESD PETG is utilised in numerous applications thanks to its excellent mechanical and chemical properties, and in particular, its ability to dissipate electrostatic charges. In the field of 3D printing, ESD PETG is valued for its ease of printing and impact resistance, making it ideal for the production of prototypes, functional components, and decorative objects that also require protection against electrostatic discharges.
In industrial settings, ESD PETG is used for manufacturing components that must operate in environments with the presence of oils and greases, thanks to its chemical resistance. This makes it ideal for pipes, fittings, and mechanical parts in sectors such as automotive, where it is essential to prevent the accumulation of electrostatic charges that could interfere with the operation of electronic devices.
In the electronics field, ESD PETG is employed to produce housings, enclosures, and printed circuit board components that require effective protection against electrostatic discharges, thereby ensuring the safety and reliability of sensitive devices. Additionally, in its ESD variant, the material is used in ATEX environments, where preventing electrical sparks is fundamental to avoid explosions in potentially hazardous atmospheres.
Finally, ESD PETG is also used in applications involving friction components, where impact resistance and electrostatic charge dissipation are crucial. For example, moving parts of industrial machinery, cable supports, and components of automation systems benefit from the properties of this material, enhancing the efficiency and operational longevity of devices.
QUOTE IN 1 SECOND WITHOUT COMMITMENT
HOW MUCH DOES IT COST TO MAKE YOUR PETG ESD PIECES?
Upload your 3D file now and discover it immediately
free instant quote