Aluminium 2017A
Also known as T451, aluminium 2017A is a 2000-series alloy characterised by high mechanical strength and good machinability, making it ideal for high-performance applications in the aerospace, automotive, and industrial sectors.
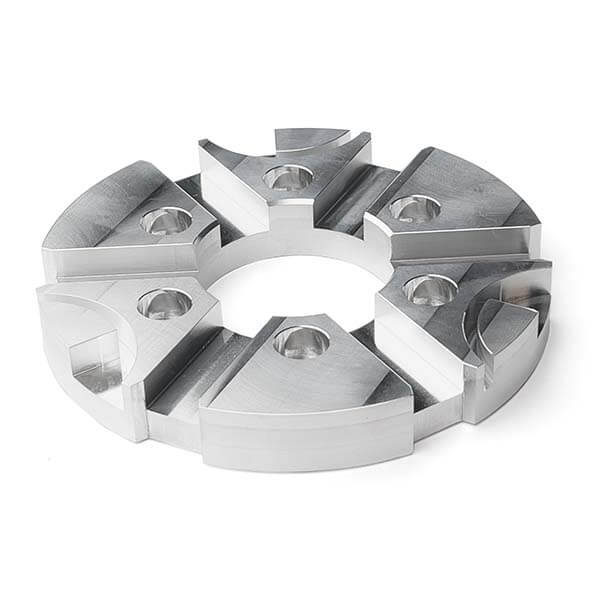
PROS
- High mechanical strength
- Good machinability
- Good fatigue resistance
CONS
- Low corrosion resistance in a marine environment
- Limited weldability
MAIN FEATURES
- Machining process: CNC Machining
- Tolerances: ISO 2768-1 fine (f) or medium (m) class. Info
- Max size: 700x700x500 mm ; 27.6x27.6x5.9 in
- Lead time: <4 days
Aluminium 2017A CNC machined VIDEO GALLERY
High Mechanical Strength
Aluminium 2017A, renowned for its high copper content, offers impressive mechanical strength compared to other aluminium alloys. With a tensile strength reaching up to 415 N/mm², this alloy can withstand substantial loads without deforming, making it ideal for structural applications that demand robustness and reliability. This characteristic makes it particularly suitable for components subjected to high static and dynamic stresses, such as in aerospace structures or precision mechanical systems. The combination of lightness and strength enhances the overall performance of projects in which it is employed.
Good Machinability
The machinability of aluminium 2017A is another key advantage that makes it a popular choice across various industrial sectors. The alloy responds well to milling, turning, and drilling operations, ensuring easy processing and high-precision results. This aspect is particularly beneficial in the production of complex or customised components, where maintaining tight tolerances is essential. Although it tends to produce long chips during machining, proper machine tool configuration can mitigate this issue. Its excellent machinability makes it ideal for high-precision moulds and intricate mechanical parts used in industries such as automotive and fashion.
Excellent Fatigue Resistance
One of the standout features of the 2017A alloy is its exceptional fatigue resistance. This property allows the material to maintain its performance even when subjected to cyclic loads or continuous vibrations over time. It is particularly valuable for components operating under repeated stress conditions, such as machinery parts, aerospace structures, and hydraulic systems. The ability to resist degradation under repeated stress not only extends the component’s lifespan but also enhances the safety and reliability of the entire system. This makes 2017A an indispensable choice for critical applications where fatigue resistance is paramount.
Image gallery
QUOTE NOW YOUR T451 ALUMINIUM PARTS
free instant quoteCOMMENT
Aluminium is an essential material in numerous industrial sectors due to its light weight, versatility, and ability to enhance its properties through the addition of alloying elements. The 2000 series, to which the 2017A alloy belongs, is notable for its high copper content, which provides mechanical strength and good performance under stress. This aluminium alloy is often used in applications where a combination of strength and reliability is crucial.
Pros
High Mechanical Strength: Aluminium 2017A is distinguished by its high tensile strength, which can reach approximately 415 N/mm². This feature makes it ideal for applications requiring materials capable of withstanding significant loads without deformation.
Good Machinability: Another key advantage is the ease with which this alloy can be machined. Cutting, drilling, and milling operations are straightforward, making the material suitable for complex components and precision machining.
Good Fatigue Resistance: Aluminium 2017A maintains its properties even when subjected to cyclic stress, such as in components exposed to vibrations or repeated loads.
Cons
Moderate Corrosion Resistance: Compared to other aluminium alloys, such as those in the 5000 or 6000 series, 2017A offers lower corrosion resistance. In aggressive or humid environments, protective coatings or surface treatments are often required to prevent degradation.
Limited Weldability: While 2017A can be welded, the process requires special precautions to avoid defects such as cracks or strength loss in the welded area. This presents challenges for applications that rely on welded joints.
Comparison with Other Aluminium Alloys
Aluminium 2017A belongs to the 2000 series family of alloys, which are characterised by their high copper content, making them particularly suitable for contexts requiring high mechanical strength. However, a closer comparison with other aluminium alloys highlights its peculiarities compared to common alternatives:
2017A vs. 2024: Both alloys belong to the same family and share a similar chemical composition, but 2024 surpasses 2017A in mechanical strength. With higher yield strength and tensile strength, 2024 is preferred for highly stressed structural applications, such as military aircraft. However, 2017A offers superior machinability, simplifying manufacturing and maintenance processes.
2017A vs. 5000-Series Alloys: 5000-series alloys, based on aluminium-magnesium, are renowned for their excellent corrosion resistance, especially in marine or humid environments. For example, 5754 is ideal for marine and automotive applications where corrosion resistance is crucial. However, 2017A significantly outperforms 5754 in mechanical strength, making it better suited for structural components requiring robustness.
2017A vs. 6061: 6061 is a widely used alloy known for its balanced combination of mechanical strength, corrosion resistance, and weldability. Compared to 2017A, 6061 has lower strength but greater ductility and better welding properties. This makes it a common choice for general applications, such as welded structures and lightweight frames. Conversely, 2017A is preferred for high-stress applications where weldability is less critical.
2017A vs. 6082: 6082, another 6000-series alloy, is valued for its excellent corrosion resistance and machinability. It is often used in marine applications and industrial structures. However, 2017A excels in fatigue resistance and overall strength, making it more suitable for mechanical components subjected to high cyclic loads.
2017A vs. 7075: Enriched with zinc, 7075 is one of the strongest aluminium alloys available, offering superior mechanical strength and hardness. However, this comes at the cost of reduced machinability and corrosion resistance. 7075 is commonly used in high-end aerospace and military applications where cost is secondary to performance. In contrast, 2017A provides a more cost-effective and machinable alternative while still offering excellent strength for a wide range of applications.
This technical comparison highlights how the choice of alloy depends heavily on specific application requirements. 2017A excels in contexts requiring a balance of high mechanical strength and good machinability, while other alloys may be preferred for their specific qualities, such as corrosion resistance or weldability.
Applications
Aerospace Components: Due to its combination of light weight and high strength, 2017A is used in the production of aircraft structures and parts. This includes structural elements such as panels, fittings, and frames, where low weight and robustness are essential for efficiency and safety. Additionally, its high fatigue resistance enables it to withstand the cyclic stresses experienced by aircraft in flight.
Hydraulics: Its mechanical properties and fatigue resistance make it suitable for hydraulic components such as cylinders and pistons. In these applications, the material’s ability to endure high pressures and repeated load cycles is crucial. The alloy is often chosen for precision and durability in demanding operational conditions.
Injection Moulds: It is valued for the production of rubber and plastic moulds, where strength and precision are essential. 2017A is used not only for standard moulds but also for customised solutions tailored to large-scale industrial production. Its ability to maintain tight tolerances during machining makes it ideal for high-precision components.
Footwear and Fashion Moulding: Specifically, it is used for moulds in the production of boots, EVA bags, and soles, demonstrating great versatility in the fashion sector. The ability to create detailed and durable forms makes the alloy an ideal choice for meeting both aesthetic and functional industry demands. The machinability of the alloy allows moulds to be customised with intricate details, improving the quality of the final product.
Automotive Sector: Aluminium 2017A is often used in the manufacture of structural and mechanical vehicle components, such as brackets, mounts, and engine parts. The combination of strength and light weight is essential for improving vehicle performance, reducing fuel consumption, and ensuring safety. Additionally, its ability to withstand high mechanical stresses makes this alloy ideal for high-performance vehicle applications.
Mechanical Industry: In the general mechanical sector, the alloy is employed in the production of machinery and equipment requiring high strength, precision, and durability. Its versatility allows its use in a wide range of applications, from industrial machine components to precision tools.
Hot Forging: Due to its excellent machinability, 2017A is used in hot forging for producing complex components. Its ability to retain strength even after heat treatment makes it ideal for applications requiring both robustness and precision.
Conclusions
Aluminium 2017A is an excellent solution for applications requiring a combination of high mechanical strength and good machinability. However, its limitations in corrosion resistance and weldability necessitate a thorough evaluation of operating conditions before selecting it as the primary material. Compared to other aluminium alloys, 2017A stands out as a versatile and competitive choice, though it may not always be the most suitable for every application.
Ultimately, 2017A is a valuable alloy for sectors such as aerospace, hydraulics, and industrial moulding, and it continues to be appreciated for its balance of mechanical properties and ease of machining. A deep understanding of its characteristics and comparison with other alloys is essential to optimise performance and reduce production costs.
ALUMINIUM 2017A PROPERTIES
Tensile breaking load | 360-415 MPa |
Modulus of elasticity | 72 GPa |
Elongation at break | 6-15 % |
Density | 2,78 g/cm³ |
Melting temperature | 510-640 °C |
Hardness | 110 HB |
Yield strength | 240-270 MPa |
Questions and answers
The 2017A alloy is an aluminium alloy belonging to the 2000 series, characterised by a high copper content as its main alloying element. This composition gives the material remarkable mechanical strength, making it suitable for applications requiring high robustness. It is commonly used in industries such as aerospace, automotive, and the production of injection moulds for rubber and plastic.
Aluminium 2017A is an alloy known for its high mechanical strength, with a tensile strength reaching approximately 415 N/mm² and a yield strength of 270 N/mm². It offers good machinability, facilitating cutting, drilling, and milling operations, making it ideal for complex components and precision machining. Additionally, it exhibits good fatigue resistance, maintaining its mechanical properties even under cyclic stresses or repeated loads. However, its corrosion resistance is moderate, being lower than that of other aluminium alloys, which makes protective coatings advisable in aggressive or humid environments.
The weldability of the 2017A alloy is limited and requires specific precautions to prevent defects such as cracks or loss of strength in the welded area. Among its other properties, it has a Brinell hardness of 110, a thermal conductivity ranging between 125 and 140 W/m·K, an elastic modulus of 72,000 N/mm², and a specific weight of 2.78 g/cm³.
Although both alloys belong to the 2000 series and have copper as their main alloying element, they have some key differences. Aluminium 2024 offers superior mechanical strength compared to 2017A, with a tensile strength reaching approximately 470 N/mm² and a yield strength of 325 N/mm². However, 2017A is generally easier to machine than 2024, which can simplify manufacturing and maintenance processes.
The 2024 alloy is often preferred for highly stressed structural applications, such as aerospace components, while 2017A is chosen when a balance between high mechanical strength and good machinability is required.
The 2017A alloy is primarily composed of aluminium, with a significant copper content ranging between 3.5% and 4.5%, which is responsible for its high mechanical strength. It also contains manganese in a proportion of 0.4% to 0.8%, which enhances its fatigue resistance. Small amounts of magnesium, ranging between 0.4% and 0.8%, contribute to the material’s tensile strength and hardness.
Other minor elements, such as iron, silicon, zinc, and titanium, are present in trace amounts and influence the overall properties of the alloy.
QUOTE IN 1 SECOND WITHOUT COMMITMENT
DON'T WAIT: UPLOAD YOUR 3D FILE AND GET A QUOTE FOR YOUR PARTS NOW!
Upload your 3D file to get one step closer to manufacturing your parts.
free instant quote