Aluminium 2011
Aluminium alloy 2011 is mainly used in precision parts such as screws and bolts. It is composed by additions of aluminium and copper that improve its hardness and strength.
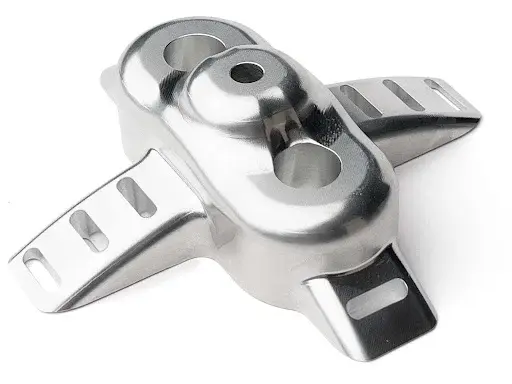
PROS
- Superior Machinability
- Hardness and Strength
- Good Surface Finish
CONS
- Average Corrosion Resistance
- Low weldability
MAIN FEATURES
- Machining process: CNC Machining
- Tolerances: ISO 2768-1 fine (f) or medium (m) class. Info
- Max size: 150x150x500 mm; 5.9x5.9x19.7 in
- Lead time: <4 days
Aluminium 2011 CNC machined VIDEO GALLERY
Top machinability
Its superior machinability enables precision parts with an excellent surface finish, ensuring functionality and aesthetics for end users. The high production speed also ensures a constant supply of parts and can potentially reduce costs.
Hardness and Strength
Its greater hardness and strength helps to create durable and resilient parts. It means that parts made with this alloy can withstand greater wear and tear, increasing the longevity of end products and reducing the replacement frequency of parts, giving users both reliability and confidence.
Good Surface Finish
A good surface finish on Aluminium 2011 parts enhances the aesthetic appearance. It means that products not only perform well, but also look clean and professional. In addition, a smooth surface can reduce the accumulation of dirt and grime, making it easier for users to maintain.
ALUMINIUM 2011 IMAGE GALLERY
QUOTE NOW YOUR ALUMINIUM 2011 PARTS
free instant quoteCOMMENT
The 2011 aluminium alloy is known for its excellent machinability. Mainly used for precision parts such as screws and bolts, it is composed of aluminium with copper added to improve hardness and strength. However, it has limited corrosion resistance and is not ideal for welding.
Pros
Excellent Machinability: Aluminium 2011 alloy is known for its excellent machinability, making it ideal for the production of precision parts such as screws and bolts. Its ability to be easily and precisely formed contributes to the production of high-quality components.
Hardness and Strength: Thanks to the addition of copper, this alloy offers greater hardness and strength than pure aluminium. This means that components made from this alloy are stronger and more durable, suitable for applications requiring greater mechanical strength.
Good Surface Finish: Finished products made from Aluminium 2011 alloy have a clean and professional surface finish. This is important not only for the aesthetic appearance of the components, but also for their functionality, as a well-finished surface can influence corrosion resistance and suitability for specific applications.
Cons
Corrosion Resistance: A significant disadvantage of the 2011 aluminium alloy is its poor corrosion resistance. This makes this alloy less suitable for applications where contact with corrosive agents such as water or chemicals is frequent. It is important to consider this limitation when choosing this alloy for a specific application.
Weldability: Due to its chemical composition, the 2011 aluminium alloy is not considered ideal for welding. This can represent a challenge for manufacturing processes that require the use of welding to join components. The difficulty in welding this alloy can limit design and manufacturing options, especially in industries where welding is a common method for component assembly.
Comparison to other materials and aluminum alloys
Lightweight: Compared to materials such as steel or brass, Aluminium 2011 is lighter, making it an ideal choice when weight reduction is an important consideration. This makes it particularly suitable for applications where the overall weight of components needs to be reduced without compromising strength and durability.
Machinability and production costs: Aluminium 2011's excellent machinability can lead to significant savings in production costs, especially in high-speed processes. Its ability to be easily shaped and machined allows for efficient and rapid production of precision components, helping to reduce production time and associated costs.
Differences compared to other aluminium alloys: When compared to other aluminium alloys such as 6061 or 7075, Aluminium 2011 offers superior machinability. However, it lacks corrosion resistance and weldability, which are important characteristics to consider in applications where durability and the ability to withstand the environment are crucial. Therefore, the choice between Aluminium 2011 and other alloys will depend on the specific needs of the application, balancing the advantages of machinability with the limitations of corrosion resistance and weldability.
Common and recommended uses
It is important to carefully consider the specific requirements of the application before using Aluminium 2011. Although it is ideal for certain situations due to its machinability and strength, its limitations, such as corrosion resistance and weldability, must also be considered. In some cases, it may be necessary to balance the advantages of workability with the strength and durability requirements of the finished component. Therefore, the choice of Aluminium 2011 should be based on a comprehensive evaluation of the application's requirements and its specific characteristics.
Production of precision parts: Aluminium 2011 is particularly suitable for the production of precision parts requiring complex machining, such as gears, screws and bolts. Its excellent machinability allows for precise and complex details, making it ideal for components that require tight tolerances and complex geometries.
Automotive, aerospace and electronics industries: This alloy is used in industries where precise, high-strength components are required. Industries such as automotive, aerospace and electronics benefit from the use of Aluminium 2011 for the production of parts that must withstand high mechanical stresses and require precision in dimensions and machining.
Conclusion
In conclusion, the 2011 aluminium alloy offers a number of significant advantages, including its exceptional machinability that makes it ideal for the production of precision parts such as screws and bolts, as well as the increased hardness and strength achieved through the addition of copper. However, it is also important to consider its limitations, such as limited corrosion resistance and poor weldability. When compared to other aluminium alloys, Aluminium 2011 offers superior machinability, but lacks corrosion resistance and weldability, which could influence the choice based on the specific needs of the application. Furthermore, while it is widely used in the automotive, aerospace and electronics industries for the production of precise, high-strength components, it is important to carefully evaluate the requirements of the specific application before using it, taking into account its advantages and limitations. Ultimately, Aluminium 2011 is an excellent choice for the production of precision parts, but its usefulness depends on careful consideration of the requirements of the application and management of its unique characteristics.
"I had a fantastic experience with Weerg for our Aluminum 2011 parts. Their expert handling of this alloy resulted in high-quality, precision components with excellent hardness, strength, and surface finish. The process was efficient, with impressive turnaround times. Weerg's transparency about the alloy's limitations was appreciated. Overall, Weerg earns a 5-star rating for its outstanding service and product quality. Looking forward to more projects together."
ALUMINIUM 2011 PROPERTIES
Tensile breaking load | 245 MPa |
Modulus of elasticity | 70 GPa |
Elongation at break | 9% |
Density | 2,83 g/cm³ |
Melting temperature | 640°C |
Hardness | 110 HB |
Yield strength | 200 MPa |
Questions and answers
Aluminum 2011 is an aluminum alloy with excellent machinability, making it particularly suitable for high-precision mechanical machining. This alloy is characterized by good mechanical strength, excellent surface finish, and high machining speed. However, compared to other aluminum alloys, aluminum 2011 has lower corrosion resistance and is not suitable for applications in humid or marine environments without additional treatments.
Aluminum 2011 is considered one of the easiest materials to machine with CNC equipment due to its excellent dimensional stability and the ability to achieve high-precision details. Its high machining speed makes it ideal for series production and components requiring tight tolerances. Additionally, a high-quality surface finish can be achieved without the need for additional processing.
Aluminum 2011 is widely used in industries such as automotive, aerospace, and electronics. It is ideal for the production of precision mechanical components such as connectors, valves, joints, and instrument parts. Its machinability makes it particularly suitable for complex components requiring precise details and reduced production times.
Aluminum 2011 offers several advantages over other aluminum alloys, including exceptional machinability, high precision in CNC machining, and the ability to achieve a high-quality surface finish without the need for additional treatments. However, it also has some disadvantages, such as lower corrosion resistance compared to other alloys like aluminum 6061, and reduced suitability for applications in outdoor or marine environments without specific treatments.
Aluminum 2011 has a typical tensile strength of approximately 380 MPa and a yield strength of 320 MPa. The Brinell hardness is about 120 HB. These characteristics make it ideal for components requiring good mechanical robustness combined with excellent machinability.
QUOTE IN 1 SECOND WITHOUT COMMITMENT
DON'T WAIT: UPLOAD YOUR 3D FILE AND GET A QUOTE FOR YOUR PARTS NOW!
Upload your 3D file to get one step closer to manufacturing your parts.
free instant quote