Aluminium 7075
Ergal: the strongest aluminium alloy
Known as Ergal, aluminium 7075 is one of the strongest alloys available. It is ideal for critical applications in the aerospace, marine, and industrial sectors, where lightness and high mechanical performance are essential.
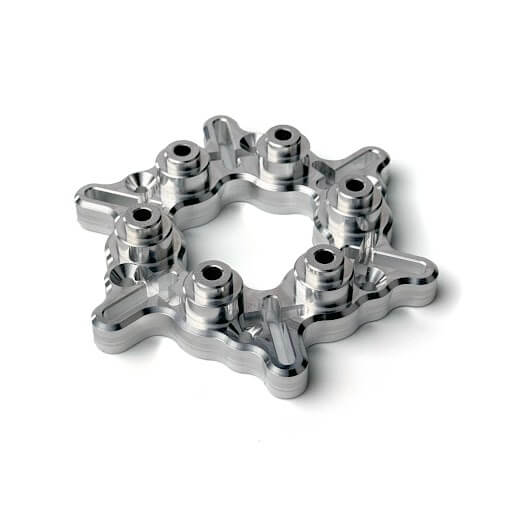
PROS
- High strength-to-weight ratio
- Excellent fatigue strength
- Good machinability
CONS
- It can easily corrode
- High cost compared to other alloys
- Difficult to weld
MAIN FEATURES
- Machining process: CNC
- Tolerance: ISO 2768-1 fine (f) or medium (m) classes. Info
- Max size: 500 x 500 x 300 mm; 19.7 x 19.7 x 11.8 in
- Lead time: <4 days
ALUMINIUM 7075 CNC MACHINED VIDEO GALLERY
Top strength-to-weight ratio
The main advantages of having an exceptional strength-to-weight ratio are increased performance, improved durability, and reduced weight: you get high performance, efficient, longer lasting, and lighter components.
resistance to cyclic loads
This feature is crucial in the aviation industry, where increased strength allows components to withstand greater stresses and strains over time without compromising performance. Improving performance allows parts to work effectively, demonstrating better overall performance.
thermal stability
Thermal stability means greater reliability and better performance. An improved reliability means that components are not affected by temperature variations, making them ideal for use in extreme and complicated environments. Improved performance allows parts to operate more efficiently over a wide range of temperatures, leading to better overall performance.
ERGAL IMAGE GALLERY
QUOTE NOW YOUR ALUMINIUM 7075 PARTS
free instant quoteCOMMENT
The Aluminium 7075, an aluminium alloy with zinc as the main alloying element, stands as one of the most significant and employed materials in the aerospace and defence industry. Its reputation is founded upon its extraordinary strength and fatigue resistance, qualities that make it a preferred option for the most demanding and critical applications in these highly specialised and critical sectors.
Pros
Excellent strength-to-weight ratio: Compared to other common aluminium alloys such as 6061-T6 and 5083-H112, Aluminium 7075 offers superior strength. With a minimum tensile strength of at least 572 MPa, yield strength of at least 503 MPa, and elongation of at least 9%, this material provides superior mechanical performance. Its lightweight nature makes it ideal for applications where weight reduction is crucial, such as in the aerospace and automotive industries.
Outstanding fatigue resistance: Aluminium 7075 exhibits excellent fatigue resistance, allowing the material to withstand repeated loads without failure. This characteristic makes it ideal for applications subjected to cyclic stresses, ensuring durability and reliability over time.
Good machinability: The machinability of this alloy enables easy welding, machining, and forming, offering flexibility in the production process. This allows for greater versatility in the use of 7075 in a wide range of industrial applications.
Cons
Susceptible to natural corrosion: Aluminium 7075 (Ergal) is vulnerable to natural corrosion, which can be a limitation in applications exposed to corrosive environments such as marine or industrial settings. This necessitates additional precautions and, at times, special treatments to protect components from wear caused by corrosion.
Higher cost compared to other alloys: Compared to other aluminium alloys, 7075 tends to have a higher cost. This may make it an expensive choice in some production contexts, especially when more economical alternatives with satisfactory performance are available. It is therefore important to carefully assess the cost-benefit ratio when deciding to use this alloy.
Difficult to weld: Another point to consider is the difficulty in welding this alloy. This process requires specialised skills and equipment to achieve high-quality joints. The complexity of welding can influence the design and manufacture of components, necessitating additional planning and preparation during the production process.
Applications of aluminium 7075
This aluminium is widely employed across a variety of industrial sectors owing to its exceptional mechanical and physical properties.
In the aerospace and defence industry, Aluminium 7075 is the preferred choice for demanding and critical applications that require high mechanical performance and fatigue resistance. It is used in the production of structural components such as aircraft parts and defence systems, where robustness and reliability are paramount.
In the automotive industry, Ergal 7075 finds application in high-performance components like suspension arms and brake calipers. Its lightweight nature, combined with superior corrosion resistance, makes it ideal for applications requiring lightweight yet sturdy components, thereby enhancing the performance and efficiency of vehicles.
Similarly, in the marine industry, this alloy is utilised for components subjected to aggressive marine conditions, such as propeller shafts and hull plates. Its corrosion resistance makes it a reliable choice for marine applications, where protection against wear caused by saltwater is essential for component durability.
In the sporting goods sectors, it is used in the manufacture of bicycle frames, golf club heads, skis, and other sports equipment. Its combination of strength and lightweight properties makes it ideal for applications requiring durable and high-performing components, enabling athletes to achieve optimal performance during use.
Aluminium 7075 continues to be a reliable and versatile choice across a wide range of industrial sectors, where its exceptional properties contribute to enhancing the performance and durability of components in various applications.
Conclusion
The 7075 alloy is one of the most significant and widely used materials in the aerospace and defence industry, owing to its exceptional strength and fatigue resistance. These qualities make it a preferred choice for demanding and critical applications in highly specialised and critical sectors.
Among its strengths, the 7075 alloy offers an excellent strength-to-weight ratio, surpassing other common aluminium alloys and providing superior mechanical performance. Its lightweight nature makes it ideal for applications where weight reduction is crucial, such as in the aerospace and automotive industries. Furthermore, its excellent fatigue resistance allows the material to withstand repeated loads without compromise, ensuring durability over time.
However, some limitations need to be considered, such as vulnerability to natural corrosion, which requires additional precautions in applications exposed to corrosive environments, and the relatively higher cost compared to other aluminium alloys. Welding difficulty is another point of concern, as this process requires specialised skills and equipment to achieve high-quality joints, influencing the design and manufacturing of components.
Despite these limitations, Aluminium 7075 finds extensive use in various industrial sectors due to its exceptional mechanical and physical properties. In the aerospace and defence, automotive, marine, and sporting goods industries, this material is used for a wide range of applications requiring strength, reliability, and superior performance. Ultimately, the 7075 alloy remains a reliable and versatile choice, contributing to the enhancement of performance and durability of components across multiple industrial contexts.
"I recently had my parts made of Aluminium 7075 by Weerg and I was very satisfied. The quality and price were great, and the Customer Service has been excellent. I highly recommend Weerg for anyone looking for quality aluminum parts."
ALUMINIUM 7075 PROPERTIES
Tensile breaking load | 468 MPa |
Modulus of elasticity | 72 GPa |
Elongation at break | 10% |
Density | 2,81 g/cm³ |
Melting temperature | 622°C |
Hardness | 150 Brinell |
Yield Strength | 444 MPa |
"I found Weerg to be the perfect solution for aluminum parts made in Aluminium 7075. Quality, Customer Service, and price were all great. Highly recommend Weerg!"
Questions and answers
7075 aluminium is a 7000-series alloy, characterised by its significant content of zinc, magnesium, and copper. This combination gives the material exceptional mechanical strength and rigidity, making it one of the strongest aluminium alloys on the market. It is particularly renowned for its use in aerospace applications due to its ability to withstand high loads while remaining lightweight. 7075 aluminium is also valued for its machinability with CNC equipment, enabling the production of high-precision components. However, compared to other alloys in the series, it has lower corrosion resistance and often requires protective treatments to enhance its durability in harsh environments.
7075 aluminium is ideal for applications requiring high mechanical strength and lightness. It is widely used in the aerospace sector for the production of structural components such as aircraft frames, gears, and supports. In the automotive and motorcycle industries, it is used for lightweight frames, sprockets, drive shafts, and other components subjected to high loads. It is also used to build high-performance bicycle frames, where the combination of lightness and robustness is critical. In the marine sector, 7075 is employed for marine engines and other applications exposed to mechanical and environmental stresses. Additionally, it is often selected for mould production, where dimensional stability and fatigue resistance are essential.
7075 aluminium has lower corrosion resistance compared to other alloys, such as the 5000 series (e.g., 5083), which are specifically designed for marine or aggressive environments. In highly corrosive conditions, 7075 can be prone to oxidation and degradation, especially if untreated. However, this issue can be mitigated through protective surface treatments, such as anodising or the application of anti-corrosion coatings. These processes significantly improve the material's durability in harsh environments, making it a viable choice for applications exposed to extreme conditions, provided it is adequately protected.
7075 aluminium is known for its excellent mechanical properties. It has a typical tensile strength of about 570 MPa and a yield strength of about 505 MPa, placing it among the strongest aluminium alloys. The Brinell hardness is around 150 HB, giving the material significant wear resistance. The alloy also has good fatigue resistance, making it suitable for applications requiring repeated load cycles. The combination of high strength, rigidity, and hardness makes 7075 aluminium an excellent choice for structural and mechanical components that must withstand high stresses.
Compared to other aluminium alloys, such as 6061 or 5083, 7075 stands out for its superior mechanical strength and rigidity. 6061 is more versatile and offers better corrosion resistance, making it a more common choice for general-purpose and less demanding applications. On the other hand, 5083 excels in marine environments due to its high corrosion resistance but does not offer the same mechanical performance as 7075. While 7075 requires protective treatments in corrosive environments, it is unbeatable when high structural performance and lightness are needed, such as in aerospace and automotive applications. Its machinability is excellent, allowing for the production of complex and precise components using CNC machines.
QUOTE IN 1 SECOND WITHOUT COMMITMENT
DON'T WAIT: UPLOAD YOUR 3D FILE AND GET A QUOTE FOR YOUR PARTS NOW!
Upload your 3D file to get one step closer to manufacturing your parts.
free instant quote