Polyethylene
The leading thermoplastic polymer with outstanding chemical resistance, electrical insulation, and tensile strength. From films to piping systems, elevate your projects with this industry-leading material.
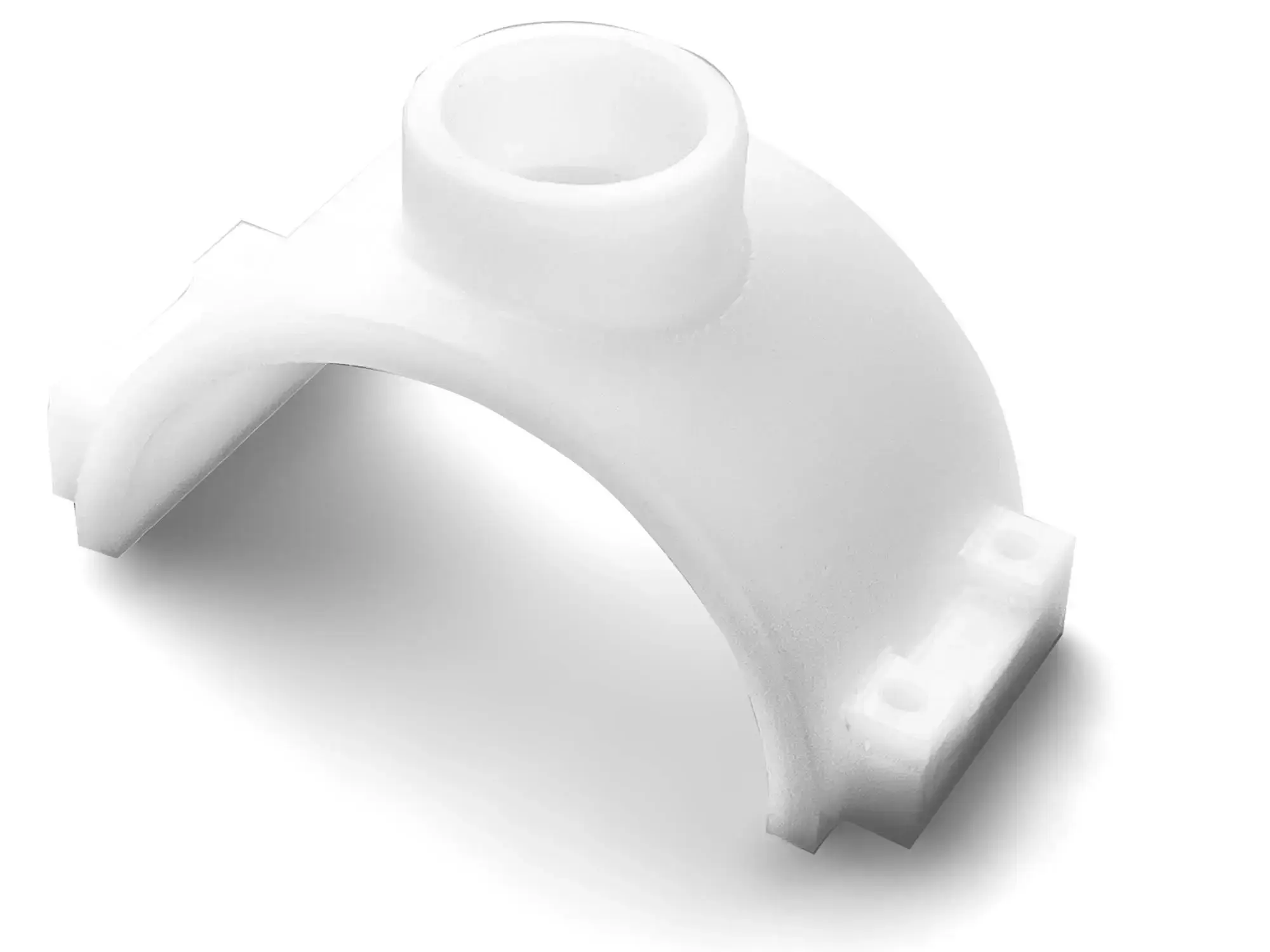
PROS
- Lightweight
- Excellent chemical resistance
- Tensile strength
- Electrical insulation
CONS
- Limited thermal resistance
- Susceptibility to UV degradation
MAIN FEATURES
- Machining process: CNC Machining
- Tolerance: ISO 2768-1 medium (m) class. Info
- Max size: 500x500x90 mm; 119.7x19.7x3.54 in
- Lead time: <4 days
POLYETHYLENE CNC MACHINED VIDEO GALLERY
Excellent chemical resistance
It is highly valued for its excellent chemical resistance, which allows it to withstand exposure to a wide range of substances without degradation. This unique property makes it an ideal choice for applications such as chemical storage containers, pipelines, and protective equipment, ensuring durability and longevity in challenging environments.
Lightweight
Its lightweight nature enables manufacturers to create thin yet durable products, such as plastic bags and packaging materials. This feature not only saves raw materials, but also contributes to waste reduction in the long run.
In the construction industry, it allows easy handling and installation of materials, such as pipes and insulation.
Electrical insulation
Its electrical insulation properties make it a popular choice in the electronics and electrical industries. Its non-conductive nature prevents the flow of electric current, providing effective protection for wires, cables, and other components. This reliable insulation capability enhances the safety and performance of electrical systems while reducing the risk of short-circuits and other related issues.
POLYETHYLENE IMAGE GALLERY
QUOTE NOW YOUR PARTS
free instant quoteCOMMENT
Experience the exceptional properties of this material, the premier choice for numerous applications in a diverse range of industries. As the most prevalent thermoplastic polymer, it exhibits superior chemical resistance, excellent electrical insulation, and remarkable tensile strength. This versatile material can meet the most demanding specifications, from high-performance films to robust piping systems.
Pros
Versatility: It is a highly adaptable material, suitable for various applications in industries such as packaging, construction, automotive, and more.
Lightweight: Its low density makes it lightweight, reducing transportation costs and facilitating ease of handling.
Durability: It has excellent chemical resistance, tensile strength, and impact resistance, ensuring long-lasting performance.
Affordability: It is a cost-effective material compared to other polymers and traditional materials, thus making it an attractive choice for many industries.
Recyclability: It can be recycled, reducing waste and contributing to more sustainable practices.
Electrical insulation: It offers excellent electrical insulation properties, making it suitable for use in cable and wire insulation.
Customizability: It can be tailored to specific requirements by modifying its density and molecular weight.
Cons
Environmental concerns: Despite its recyclability, the improper disposal of polyethylene products contributes to plastic pollution, posing a threat to ecosystems and wildlife.
Limited thermal resistance: It has a relatively low melting point, which may limit its suitability for high-temperature applications.
Susceptibility to UV degradation: Prolonged exposure to sunlight can cause it to degrade, which may require the addition of UV stabilizers to prolong its lifespan.
Permeability: It is permeable to certain gases and solvents, which may make it unsuitable for some barrier applications without additional treatment or modifications.
Applications:
Packaging: It is extensively used for flexible packaging, such as grocery bags, food packaging, shrink wrap, and films.
Construction: In the construction industry, it is used for pipes, insulation, geomembranes, and vapor barriers.
Automotive: It components can be found in fuel tanks, interior panels, and under-hood components.
Agriculture: Applications include greenhouse films, irrigation systems, and silage wrap.
Consumer goods: It is used in the manufacturing of toys, containers, bottles, and furniture.
Medical: It is utilized in medical equipment, prosthetics, and disposable syringes.
Electrical and electronics: It serves as insulation material for cables, wires, and electrical components.
Comparison with Other Materials
PVC (Polyvinyl Chloride): PVC is another widely used plastic, especially for pipes and construction materials. While both polyethylene and PVC offer excellent chemical resistance and durability, PVC has a higher rigidity and better flame resistance. However, polyethylene is more lightweight and recyclable, making it a more environmentally friendly choice in many applications.
PET (Polyethylene Terephthalate): PET is commonly used in packaging, especially for bottles. PET has a higher melting point and offers better gas barrier properties than polyethylene, making it suitable for carbonated beverage bottles. However, polyethylene is more cost-effective, lightweight, and easier to process, giving it an advantage in other packaging applications.
Polystyrene: Polystyrene is a rigid, transparent plastic used in food packaging, disposable cutlery, and insulation materials. While polystyrene offers higher clarity and stiffness, polyethylene is more flexible, durable, and resistant to moisture and chemicals.
Polypropylene: Polypropylene shares many characteristics with polyethylene, such as chemical resistance, lightweight, and recyclability. However, polypropylene has a higher melting point and better resistance to fatigue, making it suitable for applications requiring more robust mechanical properties. Polyethylene, on the other hand, has better impact resistance and is more flexible, making it ideal for films and flexible packaging.
Overall, the choice of material depends on the specific requirements of an application, with each material having its advantages and limitations. This stands out for its versatility, affordability, and recyclability, making it a popular choice in a wide range of industries.
"I recently ordered custom polyethylene parts from Weerg, and I couldn't be happier with the results. The team's expertise and attention to detail have exceeded my expectations. The pieces fit perfectly and showcase outstanding durability and chemical resistance. Weerg's exceptional service and high-quality parts have earned them a loyal customer. I highly recommend their services to anyone in need of top-notch plastic components."
Tensile breaking load | 18 MPa |
Modulus of elasticity | 750 MPa |
Elongation at break | 50% |
Flexural modulus | 1150 MPa |
HDT 0.45 MPa | 70°C |
Toughness (Charpy) | No break |
Izod impact resistance | 115 kJ/m² |
Maximum continuous use temperature | 80 °C |
"Weerg has truly impressed me with its polyethylene manufacturing capabilities. I ordered several complex parts, and the final products were nothing short of amazing. Not only were the pieces lightweight and strong, but they also had excellent electrical insulation properties, meeting all the requirements for my project. The entire process with Weerg was seamless, from design to delivery. If you're looking for a reliable partner to produce high-quality parts, you should look no further than Weerg!"
Questions and answers
Polyethylene is a thermoplastic material made from ethylene polymers, known for its lightness, versatility, and chemical resistance. It is available in different densities, such as high-density polyethylene (HDPE) and low-density polyethylene (LDPE), which differ in physical properties and applications. This material is particularly valued for its combination of mechanical strength, low coefficient of friction, and ease of processing, making it ideal for numerous industrial and commercial applications.
Polyethylene is used in a wide range of applications thanks to its versatile properties. It is employed in the food industry for the production of containers and packaging, in mechanical engineering for the creation of guides, slides, and wear-resistant components, and in the chemical industry for pipes and tanks resistant to corrosion. Additionally, it is used in the agricultural sector for irrigation systems and liners, as well as in electronics for insulators and technical components.
Polyethylene is characterized by high impact and abrasion resistance, combined with good elasticity and a low coefficient of friction. The tensile strength of high-density polyethylene (HDPE) generally ranges between 20 and 30 MPa, while the Brinell hardness is around 40-50 HB. Additionally, polyethylene is fatigue-resistant and maintains its properties even under intensive use. However, it is not particularly rigid and can deform under high loads, making it unsuitable for applications requiring high structural rigidity.
Yes, polyethylene is highly resistant to a wide range of chemicals, including acids, bases, and organic solvents. This resistance makes it ideal for applications where the material is exposed to chemically aggressive environments, such as containers for chemicals, pipes for corrosive fluids, and protective coatings. However, its resistance may vary depending on the type of polyethylene and the conditions of use, such as temperature and exposure duration.
Polyethylene has moderate heat resistance and can operate in a temperature range of -50°C to +80°C, depending on the specific type. However, it is not suitable for applications requiring high thermal resistance, as it begins to lose its mechanical properties at temperatures above 100°C. For high-temperature uses, alternative materials like polypropylene or other technopolymers with greater thermal stability might be needed.
QUOTE IN 1 SECOND WITHOUT COMMITMENT
DON'T WAIT: UPLOAD YOUR 3D FILE AND GET A QUOTE FOR YOUR PARTS NOW!
Upload your 3D file to get one step closer to manufacturing your parts.
free instant quote