PVC, CNC machined
Use CNC-machined PVC parts to achieve the full potential of your projects. They will be durable, cost-effective and more corrosion-resistant parts than other materials.
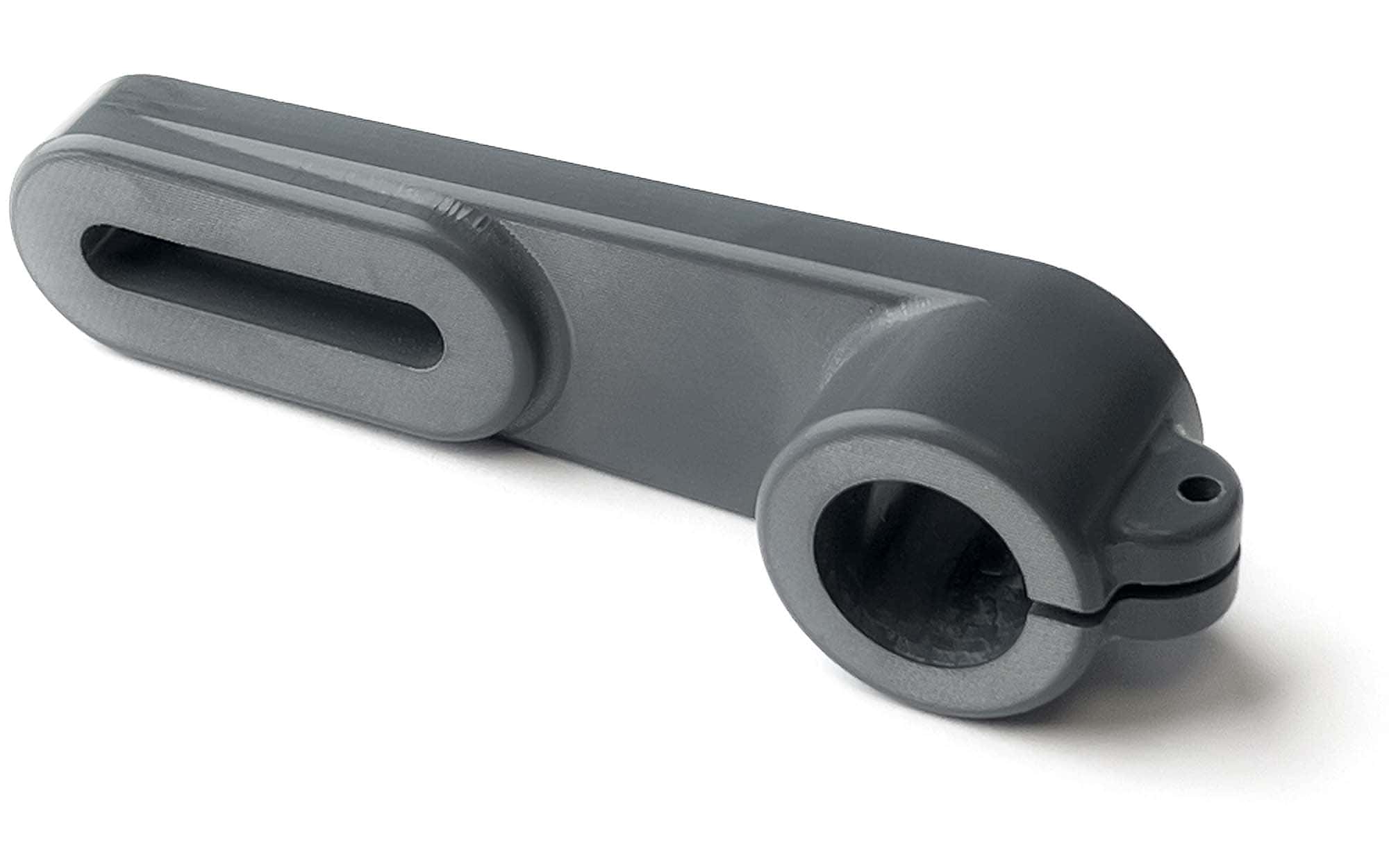
PROS
- Self-extinguishing UL94 V0
- Rigid and with good mechanical properties
- Easy to machine and weld
- Excellent electrical insulation
CONS
- Limited ductility and resilience
- Not suitable for food contact
- The maximum operating temperature is 60°C
MAIN FEATURES
- Process: CNC Machining
- Tolerance: ISO 2768-1 medium (m) class. Info
- Max size: 500x500x50mm; 20x20x2in
- Lead time: <3 days
CNC MACHINED PVC PARTS IMAGE GALLERY
COMMENT
PVC (polyvinyl chloride) is an extremely versatile and reliable material that is widely used in various sectors due to its outstanding chemical and physical properties. Its chemical stability and fire resistance make it ideal for a wide range of applications, while its good mechanical properties make it suitable for machining processes such as milling and welding. However, like any material, PVC has both advantages and disadvantages that it is important to consider.
Pros
Self-extinguishing UL94 V0: PVC is classified as self-extinguishing UL94 V0, which means it is extremely fire resistant and can self-extinguish quickly in the event of a fire, providing an additional level of safety.
Rigid and with good mechanical properties: It is characterised by rigid behaviour and good mechanical properties, making it suitable for many applications requiring strength and structural stability.
Easy to machine and weld: Due to its malleable nature, it is easy to machine and weld, enabling the fast and efficient production of complex parts with precision.
Excellent electrical insulation: This material is an excellent electrical insulator, making it ideal for applications where protection against electrical currents is required.
Durability: Thanks to CNC machining, the PVC parts are precisely manufactured and are 100% filled. This ensures that each component is manufactured exactly according to design specifications, guaranteeing high performance and long-term reliability.
Cost-effectiveness: CNC-machined PVC parts offer a great cost advantage. Their production is fast and efficient, and in most cases they are less expensive than traditional metal parts. This makes them the ideal choice for projects where cost efficiency is a priority.
Corrosion resistant: Parts made of this material are also more resistant to corrosion than metal parts. This makes them an excellent choice for applications where moisture or other corrosive elements may be present.
Cons
Limited Ductility and Resilience: PVC is not particularly ductile or resilient, which means that it may be subject to cracking or deformation under high loads or during exposure to extreme conditions. This limitation may affect its suitability for certain applications requiring greater flexibility.
Not Suitable for Food Contact: Due to the possibility of releasing harmful substances, it is not considered safe for direct contact with food or beverages. This limitation excludes it from a number of applications where some compatibility with food materials is required for health and safety reasons.
Maximum Use Temperature Limited to 60°C: One of its main limitations is its maximum use temperature, which is set at 60°C. This means that it is not suitable for high-temperature applications, as it may suffer deformation or alteration of physical properties at higher temperatures. Therefore, for applications requiring heat resistance, more suitable alternatives should be considered.
Applications of CNC-machined PVC
Automotive Industry: CNC-machined PVC is used in the production of vehicle components such as interior trim, door panels, grilles and other interior and exterior details. Its durability, corrosion resistance and ease of processing make it an ideal choice to meet the needs of the automotive industry.
Aerospace: In the aerospace sector, it is used in the manufacture of aircraft parts such as interior linings, lightweight structural components and cover panels. Its properties make it particularly suitable for aerospace applications where high performance and safety are required.
Medical Sector: PVC parts are used in the medical sector for the production of devices and equipment, such as diagnostic equipment, containers for transporting sensitive materials, and components for medical assistance devices. Their corrosion resistance and ease of sterilisation make them a preferred choice in the healthcare sector.
Electronics Sector: In the electronics sector, it is used in the production of housings for electronic devices, control panels, connectors and other components. Its electrical insulation capability and ease of processing make it a cost-effective choice for the electronics industry, where ensuring product safety and reliability is paramount.
Conclusion
PVC (polyvinyl chloride) emerges as a versatile and reliable material, widely used in various sectors due to its outstanding chemical and physical properties. Its chemical stability and fire resistance make it suitable for a wide range of applications, while its good mechanical properties make it suitable for machining processes such as milling and welding. However, it is crucial to consider both the advantages and disadvantages associated with its use.
Among its advantages are its UL94 V0 self-extinguishing classification, its rigidity and good mechanical properties, its ease of machining and welding, its excellent electrical insulation, its durability through CNC machining, and its cost-effectiveness compared to metal alternatives. In addition, PVC shows remarkable corrosion resistance, making it suitable for wet or corrosive environments.
However, its limitations must also be considered: its limited ductility and resilience that can cause cracking or deformation under high loads, its unsuitability for food contact due to the risk of releasing harmful substances, and its maximum use temperature limited to 60°C, which limits its applicability in high-temperature environments.
"I am thankful that I have had access to the excellent products and services of Weerg that have enabled me to make top quality parts with PVC."
MATERIAL PROPERTIES
Tensile breaking load | 55 MPa |
Modulus of elasticity | 3000 MPa |
Elongation at break | 10% |
Flexural modulus | 3000 MPa |
HDT 0.45 MPa | 72 ºC |
Izod impact resistance | 20 kJ/m² |
"Parts made with Weerg PVC CNC machining service are much stronger and more reliable than I imagined."
Questions and Answers
PVC (polyvinyl chloride) is a thermoplastic plastic material obtained by the polymerization of vinyl chloride. It is known for its versatility, chemical resistance, and durability. Thanks to its structure, PVC can be produced in rigid or flexible forms, making it suitable for a wide range of applications. It is also resistant to corrosion and weathering, making it ideal for both indoor and outdoor use.
PVC is used in various sectors due to its versatile properties. In construction, it is employed for pipes, gutters, cladding, and windows. In the electrical sector, it is used for cable insulation and components. It is also common in the production of flooring, wall coverings, and decorative films. Additionally, PVC is applied in the medical field for producing fluid bags, flexible tubes, and sanitary devices, thanks to its resistance and ease of sterilization.
PVC has moderate heat resistance and can operate within a temperature range of -15°C to +60°C, depending on the specific formulation. However, it is not suitable for high-temperature applications as it begins to degrade and lose structural stability above 70-80°C. For applications requiring greater heat resistance, materials like polycarbonate or polyethylene may be better alternatives.
The main difference between ABS (acrylonitrile-butadiene-styrene) and PVC lies in their mechanical and chemical properties. ABS is more rigid and impact-resistant, making it ideal for applications requiring robustness, such as automotive components and technical products. PVC, on the other hand, is more resistant to chemical corrosion and weathering, making it suitable for use in outdoor or chemically aggressive environments. Additionally, PVC is more economical and has better fire resistance compared to ABS, while ABS is lighter and easier to process. The choice between the two materials depends on the specific application requirements.
QUOTE IN 1 SECOND WITHOUT COMMITMENT
DO NOT WAIT: UPLOAD YOUR 3D FILE AND GET A QUOTE FOR YOUR PVC PARTS NOW!
Upload your 3D file to get one step closer to manufacturing your parts.
free instant quote