MJF Component Orientation
HP MJF 3D printing has enormous advantages in terms of flexibility and ability to process a wide range of complex geometries compared to other additive manufacturing technologies. MJF allows you to build objects without supports and with complex geometries without any particular process limitations.
In order to guarantee process repeatability, the finest possible results and reach the full potential of this manufacturing technology, a number of measures are required that we are going to describe briefly.
How to optimize an object for MJF 3D printing?
First of all, when designing the component, it is recommended to follow the guidelines of "design for additive manufacturing" or DfAM. These are a set of guidelines and rules, which change according to the additive technology chosen, that guide the designer in his choices, both at a macroscopic level and in small adjustments.
Another key aspect for the success of an object produced with this technology is the preparatory phase for printing by placing the object inside the printing volume of the machine. As we are going to see in this guide, in fact, finish and properties of the components can vary even considerably because of small variations.
Downwards facing surfaces (Z-)
All surfaces with an angle of less than 30° to the XY plate and facing downwards, benefit from a very uniform finish and are practically free of any signs of machining and layer scaling. In fact, the object, lying on the dust of the previous layer, receives adequate support to create itself correctly.
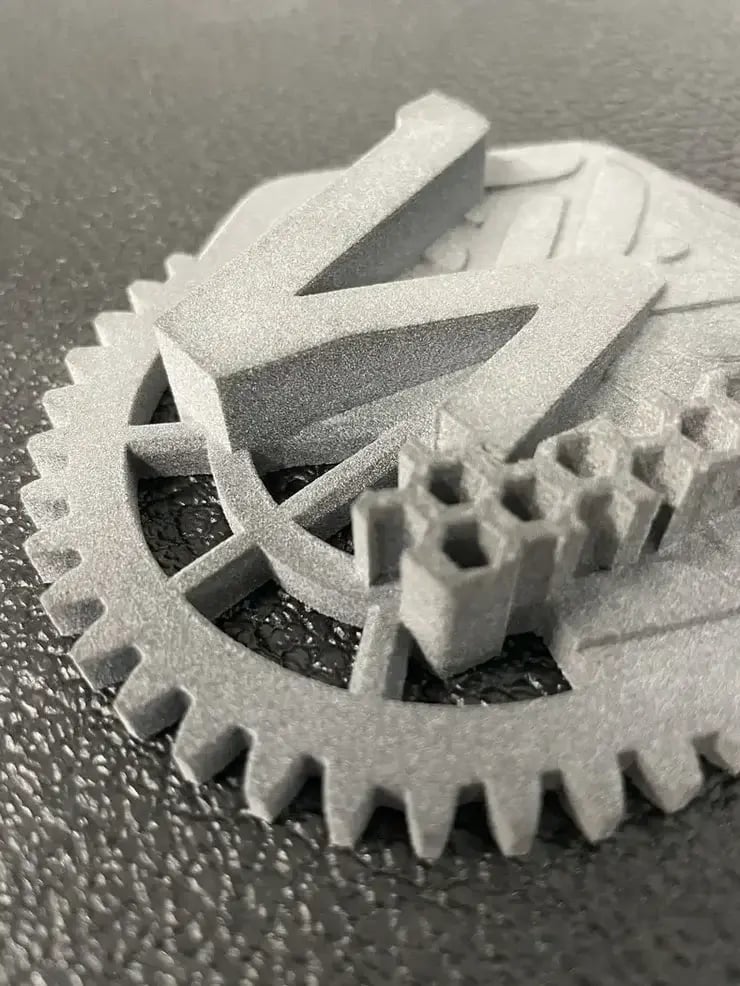
Upwards facing surfaces (Z+)
Surfaces mirroring the previous ones and therefore facing upwards (Z+), with angles of less than 30° to the XY plate, will show a much more marked scaling from the individual layers. It is also possible that these surfaces are concave, as the material cools in the central area, decreasing in volume and contracting.
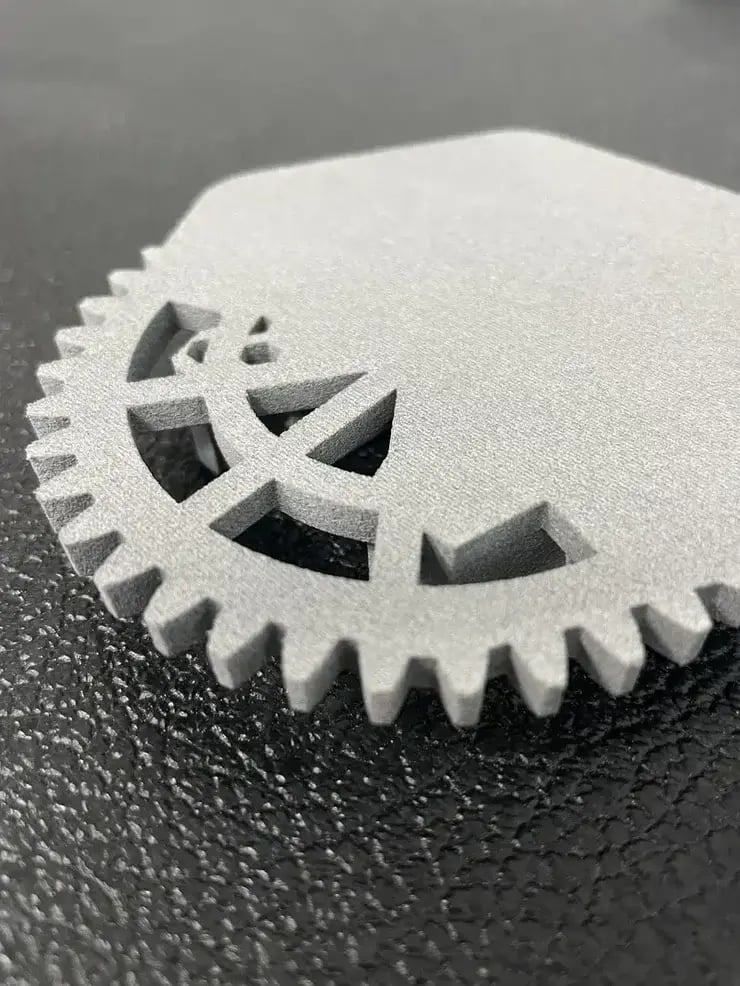
Accuracy
MJF printing process is affected by the thermal gradients created by the deposition and fusion of one layer onto another. Along the Z-axis (height) of the build, tolerances will be worse, as deformations are more difficult to control. In the XY plate, on the other hand, components and their dimensions are closer to their nominal dimensions.
Another example are cylindrical or ring-shaped objects: it would be a good idea to align their axis with the Z axis in order to have a round section in the XY plate in order to avoid deformations that could lead to a deformed elliptical section.
Resistance
Mechanical properties also change slightly between XY and Z. In fact, although the breaking stress of the components is the same along all three axes, along the Z axis the material will be less ductile, with an elongation at break reduced by approximately 50%.
Weerg's technicians check each file before fitting it into a build, considering the best orientation for its correct processing. In case your project has special needs for strength or aesthetic finishes, you can fix the original orientation in the quotation phase with the proper tick.
If you still have doubts, questions or need additional information, our team of experts is available to support you in your choice: please contact us here to discuss your project and what doubts you have about the material.