PEEK
PEEK is a polymer used in the industrial and aerospace fields with exceptional mechanical properties, very similar to those of some metal alloys. In its filament-processed version, it allows complex geometries to be obtained, leaving the designer free from most of the limitations of traditional production technologies.
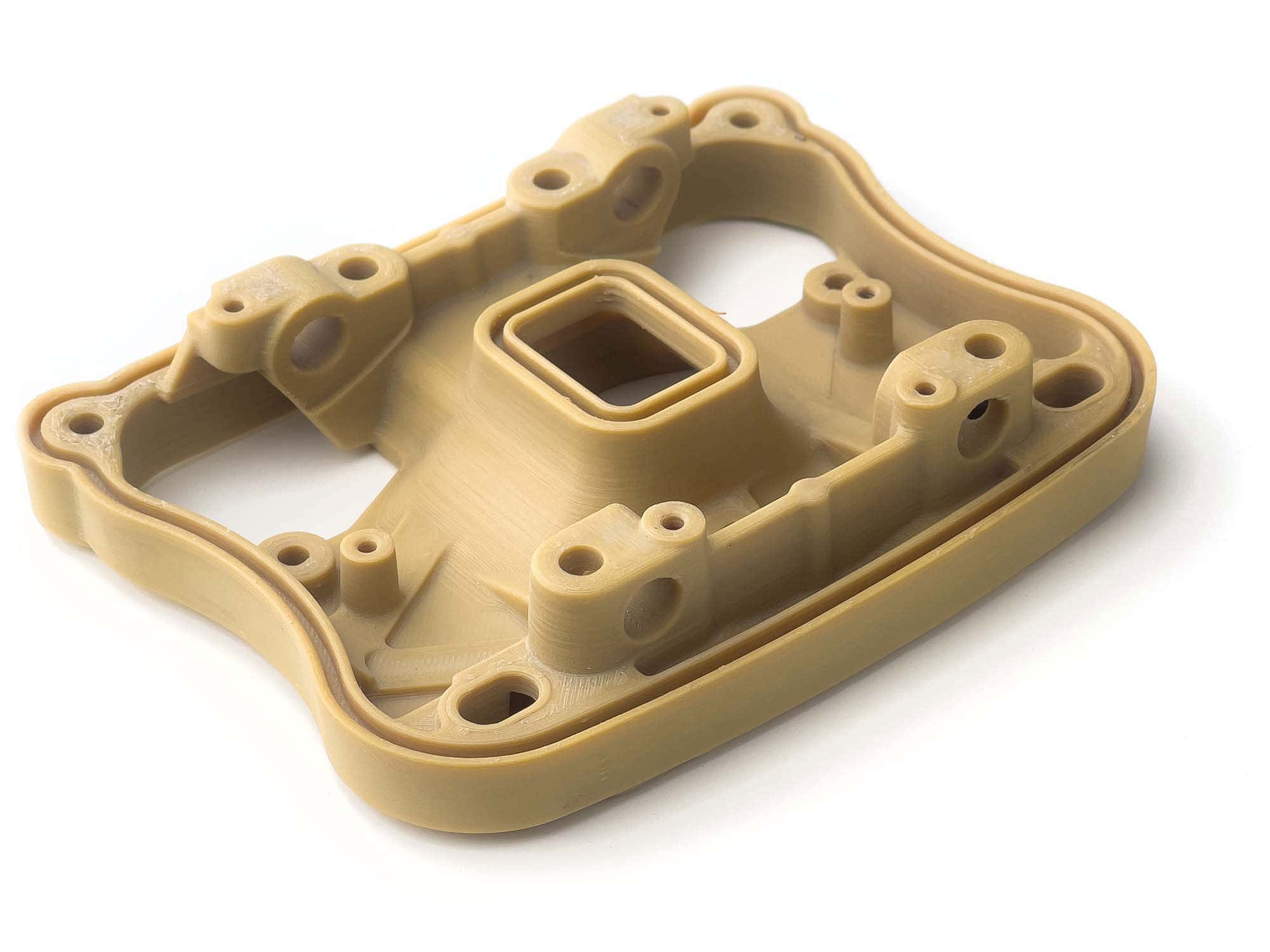
PROS
- Excellent mechanical performance
- Excellent resistance to high temperatures and chemicals
- Flame retardant
- The best option for Metal Replacement cases
CONS
- Not uniform properties on all axes
- Challenging to print
- Most expensive compared to other 3D printing materials
- Low impact resistance
MAIN FEATURES
- 3D printing process: FDM technology
- Tolerances: < 100mm ± 0,60mm; > 100mm ± 0,75%
- Max size: 300 x 300 x 400 mm; 11,8 x 11,8 x 15,8 in
- Lead time: <3 days
- Available finishes: Annealing
PEEK 3D PRINTED VIDEO GALLERY
Excellent mechanical strength
With its exceptional mechanical properties, PEEK stands out as a top choice. Its remarkable strength, makes it the ideal material for components that need to endure significant mechanical stress.
Thermal stability
With its exceptional heat resistance, this thermoplastic is the preferred choice for applications that require the ability to withstand high temperatures while maintaining their structural integrity.
Chemical resistance
With its remarkable resistance to a diverse range of chemicals, PEEK proves to be the perfect choice for applications in demanding environments, where the degradation of other materials is a concern.
PEEK IMAGE GALLERY
QUOTE NOW YOUR PARTS
free instant quoteCOMMENT
PEEK is an impressive high-performance thermoplastic used in 3D printing with FDM (Fused Deposition Modeling) technology. It presents an exceptional blend of properties, providing unparalleled mechanical strength, thermal stability, and chemical resistance.
Pros
• Exceptional Mechanical Strength
PEEK offers outstanding mechanical properties. This enhanced strength makes it an excellent choice for parts that must withstand substantial mechanical stress.
• Superior Thermal Stability
This thermoplastic provides top-tier heat resistance, making it a preferred choice for applications that need to tolerate high temperatures without compromising their structural integrity.
• Impressive Chemical Resistance
PEEK exhibits exceptional resistance to a wide variety of chemicals. This makes it suitable for applications in challenging environments where other materials might degrade.
Cons
• Cost and Processing Challenges
PEEK can be more expensive and challenging to process than some other thermoplastics. However, its superior performance can often justify the additional cost and effort.
Comparison to other PEEK VARIANTS AND HIGH-PERFORMANCE PLASTICS
When we compare PEEK to other PEEK variants and high-performance plastics, we can better understand its different characteristics.
PEEK and PEEK Annealed:
PEEK manufactured parts have a crystalline structure in an amorphous state once removed from the printer's construction surface.
They can undergo an annealing heat treatment in a thermostatic oven in which, through a controlled cycle, the material is given time to crystallize and create an organized semi-crystalline structure.
![]() PEEK Amorphous (sample part)
|
![]() PEEK Annealed (sample part)
|
Crystallinity and Mechanical Properties: Annealed PEEK has improved mechanical properties due to increased crystallinity from an additional heat treatment, resulting in higher tensile strength, stiffness, and thermal stability compared to non-annealed PEEK.
Thermal Properties: Annealed 3D printed PEEK has higher thermal stability and is more suitable for high-temperature applications compared to non-annealed PEEK, which may not perform as well under extreme temperatures.
Dimensional Stability: Annealing improves dimensional stability of 3D printed PEEK parts by relieving internal stresses that can cause warping or deformation, resulting in more accurate and stable dimensions. Non-annealed parts are more prone to these issues.
Post-processing time: Annealing adds a step to production, increasing production time. Parts that are not annealed can be produced faster, but may be less performing..
Surface Finish: Annealing can improve the surface finish of 3D printed PEEK parts by reducing roughness and irregularities.
PEEK CF and PEEK GF:
PEEK CF (Carbon Fiber) and PEEK GF (Glass Fiber) also provide excellent mechanical and thermal properties. However, the semicrystalline structure of annealed PEEK offers higher tensile strength and superior dimensional stability.
CNC Machined PEEK:
Compared to CNC machined PEEK, 3D printed PEEK allows for more complex designs and can eliminate the need for expensive tooling. However, CNC machining may provide a better finish and tighter tolerances on some parts.
Metals:
As a 'Metal Replacement' material, PEEK can provide similar strength and heat resistance to some metals, but at a fraction of the weight. This makes it an exciting option for many applications where weight reduction is essential.
Recommended applications:
PEEK's extraordinary properties make it a versatile choice across a wide spectrum of applications. Its incredible performance under harsh conditions results in high-value applications across numerous industries:
Aerospace
It's an ideal choice for aerospace applications due to its high strength-to-weight ratio, excellent heat resistance, and flame retardant properties.
Automotive
In the automotive sector, it can be used for parts requiring high strength and heat resistance, such as under-the-hood components.
Oil and Gas
Its excellent chemical resistance makes it suitable for use in oil and gas industry components exposed to harsh chemicals.
Medical
PEEK is commonly used in the medical field for surgical instruments and implantable devices due to its biocompatibility.
Chemical processing
Its strong resistance to a wide range of chemicals makes it ideal for components in chemical processing plants.
Conclusions
In summary, PEEK stands out as a valuable material in the 3D printing landscape: its superior properties ensure that it will continue to find new uses in various sectors.
"In the demanding field of aerospace engineering, PEEK from Weerg truly excels. Its strength, thermal stability, and chemical resistance exceed expectations. With Weerg's efficient service, we optimized our design and received our parts in record time. PEEK is not just a plastic, it's a game-changer, enabling us to achieve significant weight reduction without compromising on durability. A breakthrough in aerospace applications!"
MATERIAL PROPERTIES
Tensile breaking load | 100 MPa |
Modulus of elasticity | 3,7 MPa |
Elongation at break | 3% |
Flexural modulus | 3612 MPa |
HDT 0.45 MPa | 180 ºC |
Izod impact resistance | 7,1 kJ/m² |
Questions and answers
PEEK (Polyetheretherketone) is a high-performance semicrystalline thermoplastic material known for its exceptional mechanical, thermal, and chemical properties. This polymer offers a high strength-to-weight ratio, maintaining lightness and durability, characteristics that make it ideal for critical applications. PEEK resists extremely high temperatures, has excellent wear and abrasion resistance, and provides outstanding electrical insulation and chemical resistance. The combination of these features positions it among the most advanced materials for industrial and technical applications.
PEEK is used in numerous industrial sectors thanks to its versatility and high-performance properties. In the aerospace sector, it is employed to produce lightweight and durable components capable of withstanding high temperatures and mechanical stress. In the medical field, it is used for surgical implants and prostheses due to its biocompatibility and chemical stability. In the automotive industry, PEEK is utilised for components exposed to high temperatures, such as engine parts, seals, and connectors. Other applications include the production of industrial parts like gears, supports, and bearings, where wear resistance and consistent performance in aggressive environments are required. Finally, it is used in electronics for making electrical insulators and components that require dimensional stability and thermal insulation.
PEEK is known for its excellent thermal resistance. The heat deflection temperature (HDT) of semicrystalline PEEK reaches 320°C at 0.45 MPa and can operate continuously up to 250°C without losing its mechanical and dimensional properties. This ability to withstand extreme temperatures makes it suitable for applications in particularly hot environments, such as engines, turbines, and high-performance industrial equipment.
PEEK is printed using FDM (Fused Deposition Modeling) technology, a process that requires specialised equipment capable of operating at very high temperatures. For 3D printing PEEK, high-temperature extruders capable of reaching over 400°C are needed to ensure proper melting and deposition of the material. The print bed must be heated up to 150°C to maintain part adhesion during the process and prevent warping. Additionally, a heated chamber is essential to control the ambient temperature during printing, allowing gradual cooling and correct crystallisation of semicrystalline PEEK. The process requires precision and optimisation of parameters due to the material's complexity and high thermal stability.
PEEK offers numerous advantages, making it an ideal material for advanced technical applications. Its exceptional thermal resistance allows it to operate continuously up to 250°C without losing stability. It has high mechanical strength, being robust, rigid, and resistant to tensile stress and wear, offering performance comparable to some metals but with reduced weight. PEEK is also extremely resistant to aggressive chemicals, oils, and solvents, making it ideal for challenging industrial environments. Thanks to its biocompatibility, it is approved for medical applications such as surgical implants and prostheses, while its excellent dielectric properties make it suitable for electrical insulation and thermal applications. An additional advantage is its dimensional stability, enabling it to retain shape and mechanical properties even under prolonged thermal and mechanical load. This combination of features makes PEEK widely used in aerospace, medical, automotive, and industrial sectors, where lightness, strength, and durability are required in extreme conditions.
QUOTE IN 3 SECONDS WITHOUT COMMITMENT
Do you want to turn your 3D project into reality?
Upload your 3D file to get one step closer to manufacturing your parts.
free instant quote