PEEK CNC MACHINED
Our services include PEEK CNC machining on industrial grade peek. It offers 100% infill and tight tolerances for the most demanding industrial applications.
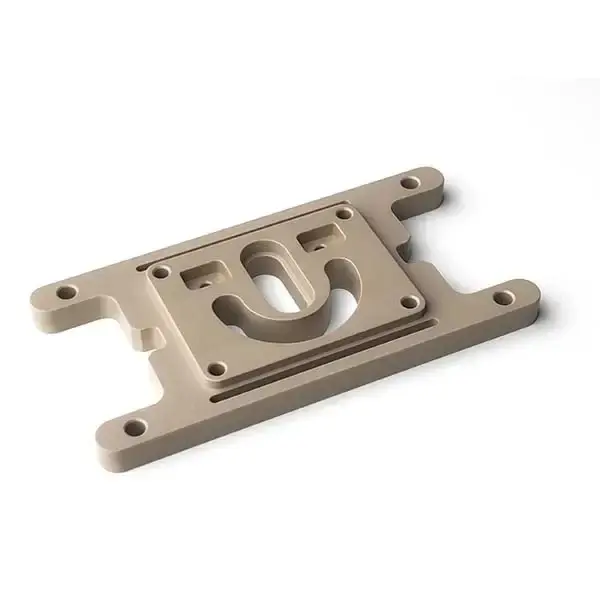
PROS
- Dimensional accuracy
- High temperature resistance
- Very high specific strength
- Flame retardant UL94 V0
- Food contact certified
CONS
- Tool marks could be visible
- Limited geometric freedom
- High cost
- Limited maximum part size
MAIN FEATURES
- Process: CNC machining
- Tolerance: ISO 2768-1 fine (f) or medium (m) class. Info
- Max size: 500x450x55mm 19,6x17,7x2,2in
- Lead time: <3 days
PEEK CNC MACHINED VIDEO GALLERY
HIGH MECHANICAL RESISTANCE
Through CNC machining, Peek further enhances its already remarkable strength properties, becoming a reliable and durable material for complex industrial applications. Precision milling contributes to strengthening the material's molecular structure, ensuring greater robustness and longevity over time.
FLAME RETARDANT UL94 V0
The preservation of the UL94 V0 fire-resistant classification even after CNC machining underscores the intrinsic robustness of Peek, confirming its reliability in high-risk fire environments. This feature makes it an ideal choice for applications requiring fire-resistant materials, thus contributing to ensuring a safe working environment compliant with the highest safety standards.
FOOD CONTACT CERTIFICATION
Peek is certified for food contact, proving to be a safe and reliable material for the food industry and related sectors, where hygiene and safety are paramount.
PEEK CNC GALLERY
MAKE YOUR PEEK CNC PARTS NOW
Upload your 3D file now and get a free instant quote
free instant quotePEEK CNC COMMENT
As part of our services, we not only 3D print Peek, but also offer advanced CNC machining for this extraordinary material. Peek, or polyetheretherketone, emerges as a high-end choice, characterised by exceptional performance. Its processing by CNC milling and turning opens up new possibilities, allowing this semi-crystalline thermoplastic to be moulded to specific requirements.
Pros
Tight tolerances: CNC machining of Peek represents a breakthrough in achieving extremely tight tolerances. This is crucial in industrial applications that require absolute precision. Peek's ability to maintain these tolerances during the CNC milling process ensures the dimensional consistency required for the most critical applications. The resulting precision allows components with complex geometries to be manufactured, satisfying the demands of advanced designs and demanding engineering challenges.
High Temperature Resistance: Peek's remarkable resistance to high temperatures is a distinctive feature that makes it particularly suitable for extreme operating environments. CNC machining, rather than compromising these thermal properties, preserves and enhances them. This means that Peek parts, even after CNC milling, can easily withstand high thermal conditions while maintaining their stability and structural integrity. This consistent resistance to high temperatures greatly expands Peek's applications in industries such as aerospace, where extreme conditions are the order of the day.
High Mechanical Strength: CNC machining of Peek represents a stage of refinement of its already exceptional mechanical strength properties. The precision milling helps optimise the molecular arrangement of the material, further improving its strength. CNC-machined Peek is thus a material that not only retains its original strength but strengthens it, offering durability and reliability in demanding industrial environments.
Flame-retardant UL94 V0: Retaining the UL94 V0 flame-retardant rating even after CNC machining confirms Peek as a safe choice in fire-risk environments. Its ability to self-extinguish contributes significantly to safety and compliance with the highest fire standards, confirming its crucial role in applications requiring fire-resistant materials.
Food Contact Certificate: Peek's food contact certification perseveres uncompromised even after CNC machining. This is crucial in sectors such as the food industry, where safety and compliance with food regulations are priorities. Peek's ability to maintain its suitability for food contact helps ensure safe and reliable applications in contexts where hygiene is paramount.
Cons
Visible Tool Marks: Although the CNC machining of Peek offers exceptional precision, it is important to consider the possibility of visible tool marks on the surface of the material. This aspect, if not handled properly, could be an aesthetic drawback. However, it is reassuring to know that with the use of advanced machining techniques and the expertise of skilled operators, this visibility can be minimised or even eliminated. Attention to detail during machining can lead to visually impeccable results, ensuring that the surface of the CNC-machined Peek retains its aesthetic integrity.
Limited Geometric Freedom: CNC machining, while offering extraordinary precision, can present certain limitations in the geometric freedom of the shapes that can be produced. This is particularly relevant in applications requiring complex geometries or special design details. However, it should be noted that with careful analysis and the use of advanced machining strategies, it is often possible to overcome these limitations. Expert advice in the design and machining phase can help maximise flexibility in creating complex shapes while maintaining the required precision.
High Material Cost: One aspect to consider when choosing CNC-machined Peek is its high cost. Despite the superior performance offered by the material, budget consideration is crucial, especially in projects with limited financial resources. A careful cost analysis, balanced with project-specific performance requirements, is essential to ensure a considered and sustainable choice.
Maximum Size Limitations: CNC machining of Peek may result in limitations in the maximum size of parts that can be produced. This size constraint must be carefully considered in applications requiring large components. In such contexts, it may be necessary to explore alternatives or assembly strategies to meet the desired dimensions. Careful planning and collaboration with CNC machining experts can help optimise the process and find effective solutions for the limited maximum Peek dimensions.
Applications of Peek CNC
CNC machining of Peek, with its outstanding characteristics, lends itself to a wide range of applications in diverse industries. In the food industry, where hygiene regulations are strict, CNC-machined Peek is used for the production of components that come into direct contact with food, ensuring safety and compliance with industry standards. The aerospace industry benefits from Peek's properties in the manufacture of structural parts, thanks to its combination of mechanical strength, light weight and ability to maintain integrity at extreme temperatures, thus contributing to the efficiency and durability of aircraft.
In the automotive sector, CNC-machined Peek presents itself as a viable alternative to metal, providing components with superior tensile strength, heat resistance and significant weight reduction. This versatility also extends to the medical field, where CNC machining of Peek is used in the production of customised medical devices, exploiting its hygienic, strength and precision characteristics.
The chemical and nuclear industries find Peek an answer to their needs for chemical and thermal resistance. Its ability to maintain structural integrity in corrosive environments and high temperatures makes it essential for the production of critical equipment and components in these applications.
In addition, Peek's CNC machining offers a unique opportunity for rapid prototyping and the production of customised components. The flexibility of this process allows the material to be adapted to the specific needs of particular projects, further expanding its application possibilities in a wide range of industries.
Conclusion
Our Peek CNC machining services stand as the meeting point between innovation and the most advanced industrial requirements. Despite the challenges that can arise, such as visible tool marks and limits in geometric freedom, CNC-machined Peek maintains its leading position in the most demanding industrial applications.
The precision guaranteed by the extremely tight tolerances is crucial for projects requiring dimensional consistency in every detail. Resistance to high temperatures remains unaffected, allowing Peek to be used in extreme operating environments, from aerospace manufacturing to the most severe industrial applications.
Despite its high cost and limited maximum size, CNC-machined Peek continues to prove its worth in projects that demand maximum performance. Relevant certifications, including UL94 V0 fire rating and food contact suitability, reinforce its position as a reliable material that conforms to the highest standards.
In summary, the combination of tight tolerances, high temperature resistance and crucial certifications makes Peek CNC an ideal choice for advanced industrial projects. Our services provide a unique balance between precision engineering and technological innovation, opening up a range of possibilities to satisfy the most demanding requirements of modern industry.
MATERIAL PROPERTIES
Tensile breaking load | 101 MPa |
Modulus of elasticity | 4,4 GPa |
Elongation at break | 20% |
Density | 1,31 g/cm³ |
At Weerg, we pride ourselves on providing fast, reliable and amazing customer service. We believe that this is what distinguishes great companies from others.
Questions and Answers
CNC-machined PEEK (Polyetheretherketone) is a high-performance semicrystalline thermoplastic material shaped through Computer Numerical Control (CNC) machining. This technique enables the production of high-precision and high-quality components. PEEK is renowned for its excellent mechanical, thermal, and chemical properties. It exhibits exceptional resistance to high temperatures, retaining its mechanical properties up to 250°C, and outstanding chemical resistance against a wide range of aggressive agents, such as acids, solvents, and bases. Additionally, it is highly resistant to wear, abrasion, and mechanical stress while remaining lightweight. Its biocompatibility also makes it ideal for medical applications.
PEEK offers a unique balance of lightness, mechanical strength, and thermal stability, making it one of the most efficient materials for CNC machining. Compared to other polymers like nylon or polycarbonate, PEEK provides greater rigidity and durability, making it suitable for critical applications. When compared to metals, PEEK is significantly lighter and does not require anti-corrosion treatments, while offering comparable mechanical strength in many cases. Furthermore, CNC machining maximises its properties by enabling the production of complex components with tight dimensional tolerances and high-quality finishes. It is particularly suited for chemically aggressive environments and high-temperature conditions, where other materials may deform or degrade.
CNC machining of PEEK offers numerous advantages over other technologies, such as 3D printing or injection moulding. With CNC machining, it is possible to achieve components with high dimensional precision, tight tolerances, and smooth surfaces without the need for additional finishing. Furthermore, CNC allows direct machining of PEEK semi-finished products, eliminating the need for costly moulds, making it an ideal choice for small batch production or functional prototypes. The versatility of CNC technology also enables the creation of complex geometries that are challenging to produce using other methods. Compared to 3D printing, CNC machining ensures higher mechanical strength and isotropy, as the material retains its original structure without layered construction.
CNC-machined PEEK is utilised in high-performance sectors such as aerospace, automotive, medical, and electronics industries. In aerospace, it is used to create lightweight yet heat-resistant structural components. In the automotive sector, it is employed to produce engine parts, bearings, and seals that must withstand intense mechanical and chemical stress. In the medical field, CNC-machined PEEK is used for surgical instruments and implants due to its biocompatibility and sterilisation capabilities. In electronics, it is valued for manufacturing insulators and protective casings, thanks to its excellent dielectric and heat-resistant properties. Additionally, it is ideal for precision mechanical components, such as gears and guides, which must operate in chemically aggressive or high-pressure environments.
QUOTE IN 3 SECONDS WITHOUT COMMITMENT
DO YOU WANT TO TURN YOUR 3D PROJECT INTO REALITY?
Upload your 3D file to get one step closer to manufacturing your parts
free instant quote